„Born to dare“, „Don’t crack under pressure“, „Live for greatness“ – jede Marke hat ihren eigenen Leitspruch, über den sie sich definiert. Die Schweizer Uhrenmanufaktur Rado, auch bekannt als der selbsternannte „Master of Materials“, folgt dem Mantra: „If we can imagine it, we can make it. And if we can make it, we will.” Doch wo genau positioniert sich Rado in einer Welt, in der Uhrenmarken mit mineralischen Faserverbundwerkstoffen und Betongehäusen herumexperimentieren? Um das herauszufinden und in die Welt der Keramikproduktion bei Rado einzutauchen, bin ich in den Zug nach Boncourt gestiegen und in die nahe gelegene Stadt Lengnau in der Schweiz gefahren.
Seit vielen Jahren vom Innovationsgeist angetrieben
Ob in der Kunst oder in der Technik, wir Menschen nutzen Keramik schon seit mehr als 20.000 Jahren. Davon zeugt beispielsweise die Venus von Dolní Věstonice, die bereits 28.000 v. Chr. entstanden ist. Zugegeben, Rados Geschichte geht nicht ganz so weit zurück, aber ihre Verwendung von Keramik hat eine zentrale Rolle in der Geschichte der Uhrmacherei gespielt. Seit der Gründung unter dem Namen Schlup & Co. im Jahr 1917 und der Umstrukturierung des Unternehmens 1957, als auch die erste Kollektion unter dem Namen Rado erschien, hat die Uhrenmanufaktur stets Wert darauf gelegt, Grenzen zu überschreiten.
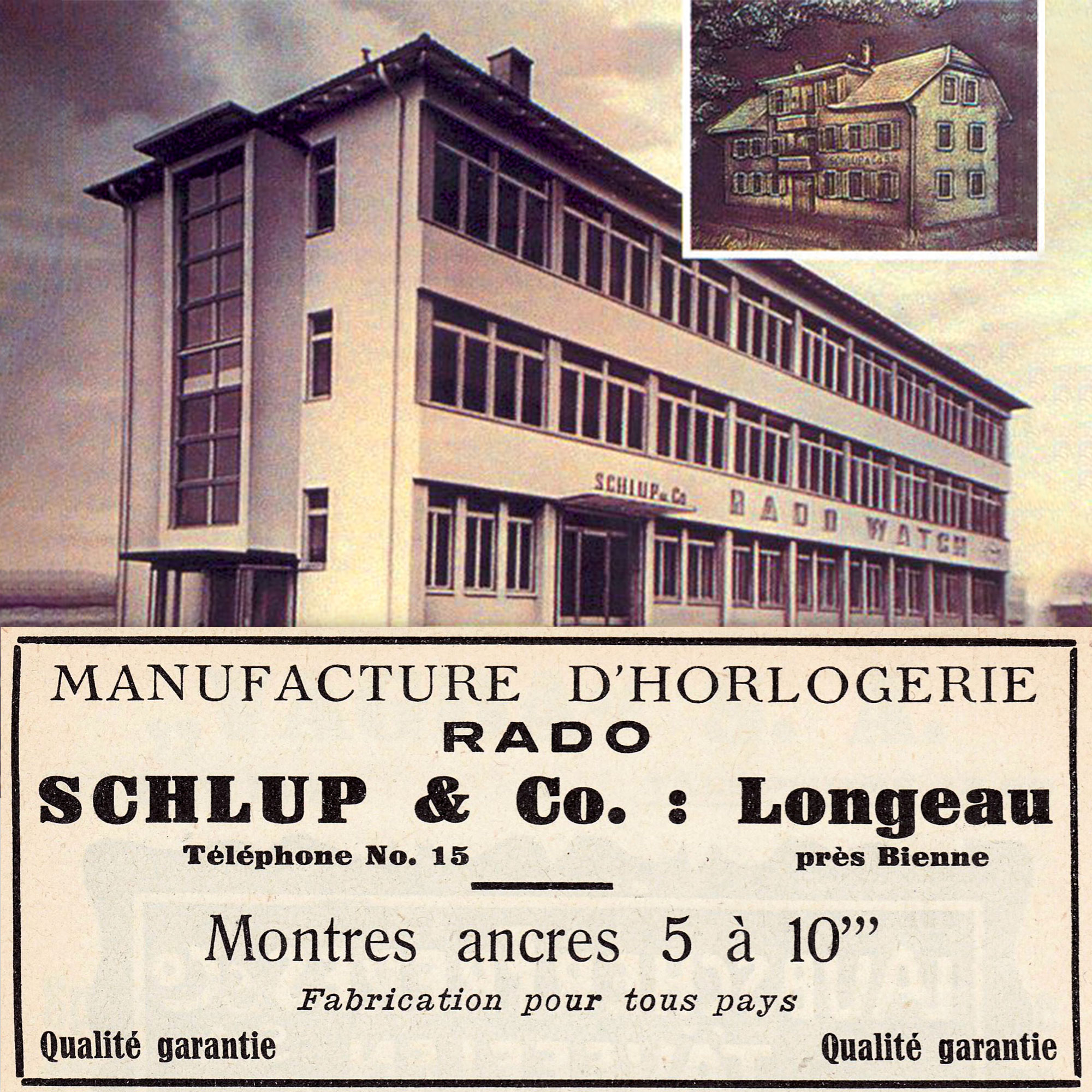
1962 war ein entscheidender Moment in der Geschichte von Rados Rolle als „Master of Materials“, als man Hartmetall für die DiaStar 1 verwendete – im selben Jahr, in dem auch die prägende Captain Cook lanciert wurde. Als erste Uhr mit einem wirklich kratzfesten Gehäuse und Saphirglas war die DiaStar 1 wegweisend für die Zukunft der Manufaktur.
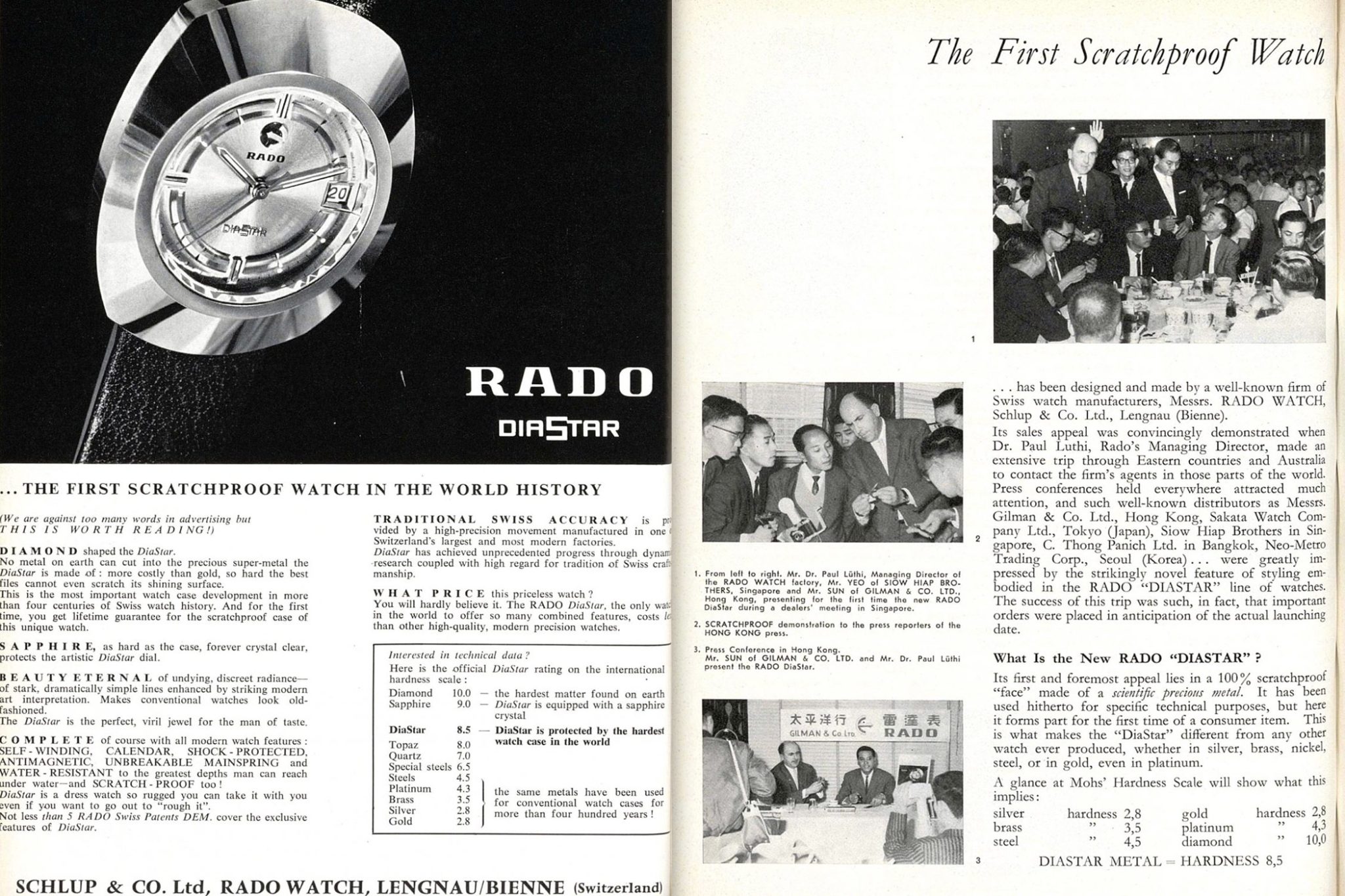
Doch das war nur der Anfang. 1986 erreichte Rado einen neuen Meilenstein mit der Einführung seiner Hightech-Keramik und läutete eine neue Ära im Bereich der Keramik ein. Die 80er kennzeichneten auch das Jahrzehnt, in dem Ceramos erfunden wurde – ein Material, das die Manufaktur erst 2011 offiziell einführte. Doch nicht nur die innovativen Materialien erregten Aufmerksamkeit: Neben ihrer markanten Ästhetik und metallisch anmutenden Oberflächen überzeugten die Zeitmesser die Kunden auch durch ihre kühle, seidige Haptik. So ergibt sich daraus auch einer der anderen Slogans von Rado: „Feel it“.
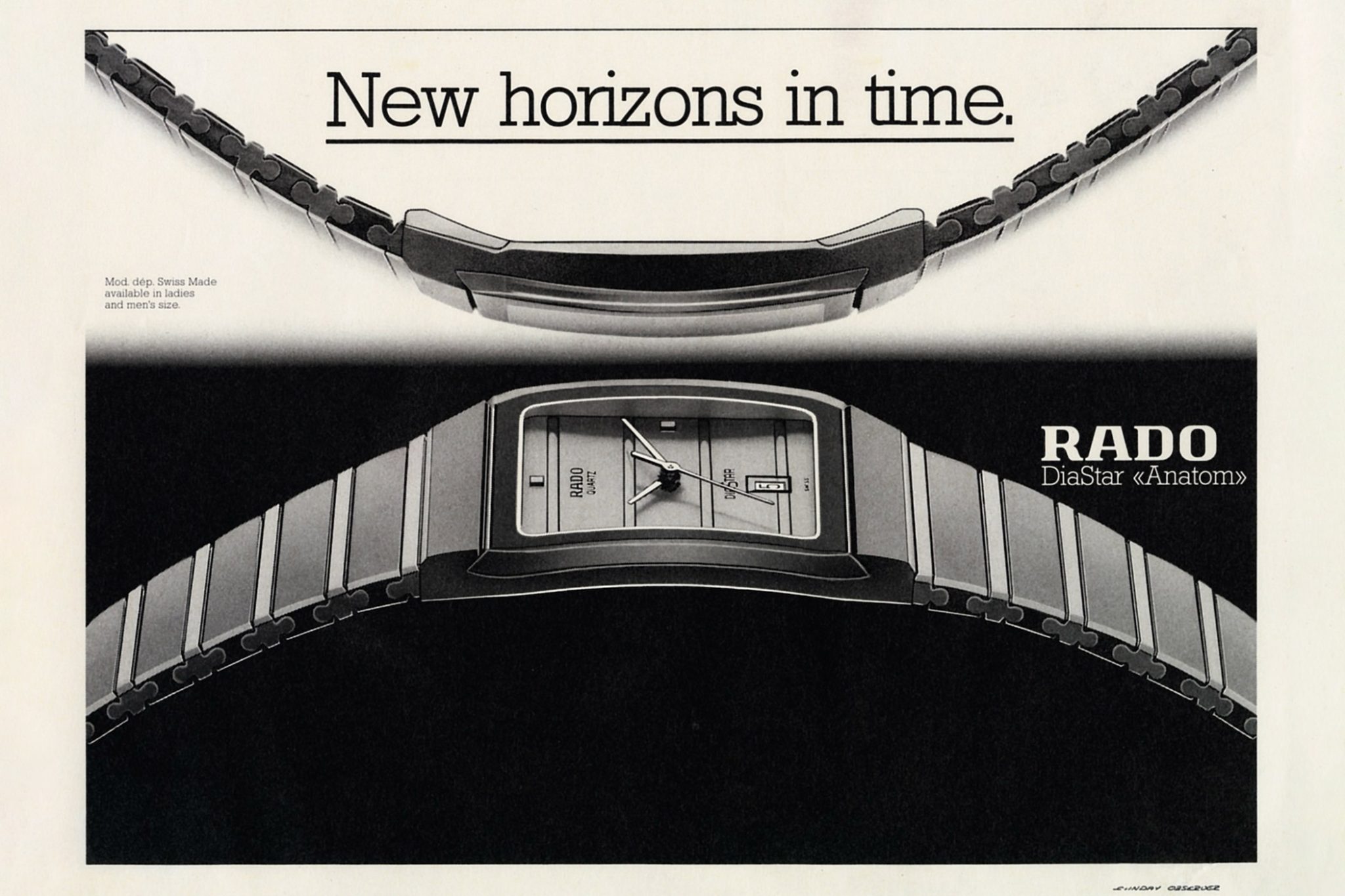
Zeitmesser sollten langlebig sein – wie passt Hightech-Keramik ins Bild?
Rado zeichnet sich zum Großteil durch seine Arbeit mit Keramik und Innovationen in diesem Bereich aus, aber welchen Status hat Hightech-Keramik in der Luxusuhrenindustrie? Gegenüber herkömmlich genutzten Materialien wie Stahl oder Edelmetallen bietet Hightech-Keramik viele Vorteile. Vor allem ist das Material unglaublich hart und gleichzeitig besonders leicht: Es ist 500 Prozent härter als Stahl, aber dennoch um 25 Prozent leichter. Im Vergleich zu 18-karätigem Gold ist es zehnmal härter, aber auch 2,5-mal leichter. Somit ist Hightech-Keramik nicht nur widerstandsfähig, sondern auch eine bevorzugte Option für diejenigen, die kein Gewicht an ihrem Handgelenk spüren wollen. Darüber hinaus ist Stahl (mit Ausnahme bestimmter Stahllegierungen, wie dem von Chopard entwickelten Lucent-Stahl) im Allgemeinen nicht hypoallergen, während Hightech-Keramik nicht nur hypoallergen ist, sondern sich auch an die Körpertemperatur des Trägers anpasst. Zudem steigert Rado die Leichtigkeit seiner Keramikuhren durch die Verwendung von Monoblock-Keramikgehäusen, die ohne einen Stahlkern auskommen.
Hightech-Keramik: Wie stellt Rado sie her?
Ein Besuch bei Comadur in Boncourt, der Manufaktur, in der die hochkeramischen Komponenten von Rado hergestellt werden, verschaffte mir einen Einblick in den Produktionsprozess des bekanntesten Materials der Marke: Hightech-Keramik. Hightech-Keramik ist, um es für die Nicht-Wissenschaftler unter uns auf den Punkt zu bringen, ein anorganisches, nicht-metallisches Material, das durch einen Brennprozess bei hoher Temperatur verfestigt wird. Sie basiert auf hochreinen Ausgangsstoffen wie Zirkonoxid, Aluminiumoxid oder Siliziumnitrid, die in Pulverform mit vollkommen gleichmäßiger Korngröße vorliegen. Hightech-Keramik spielt bei Rado seit Jahrzehnten eine wichtige Rolle und wurde erstmals 1986 auf dem Armband eines Integral-Modells eingesetzt.
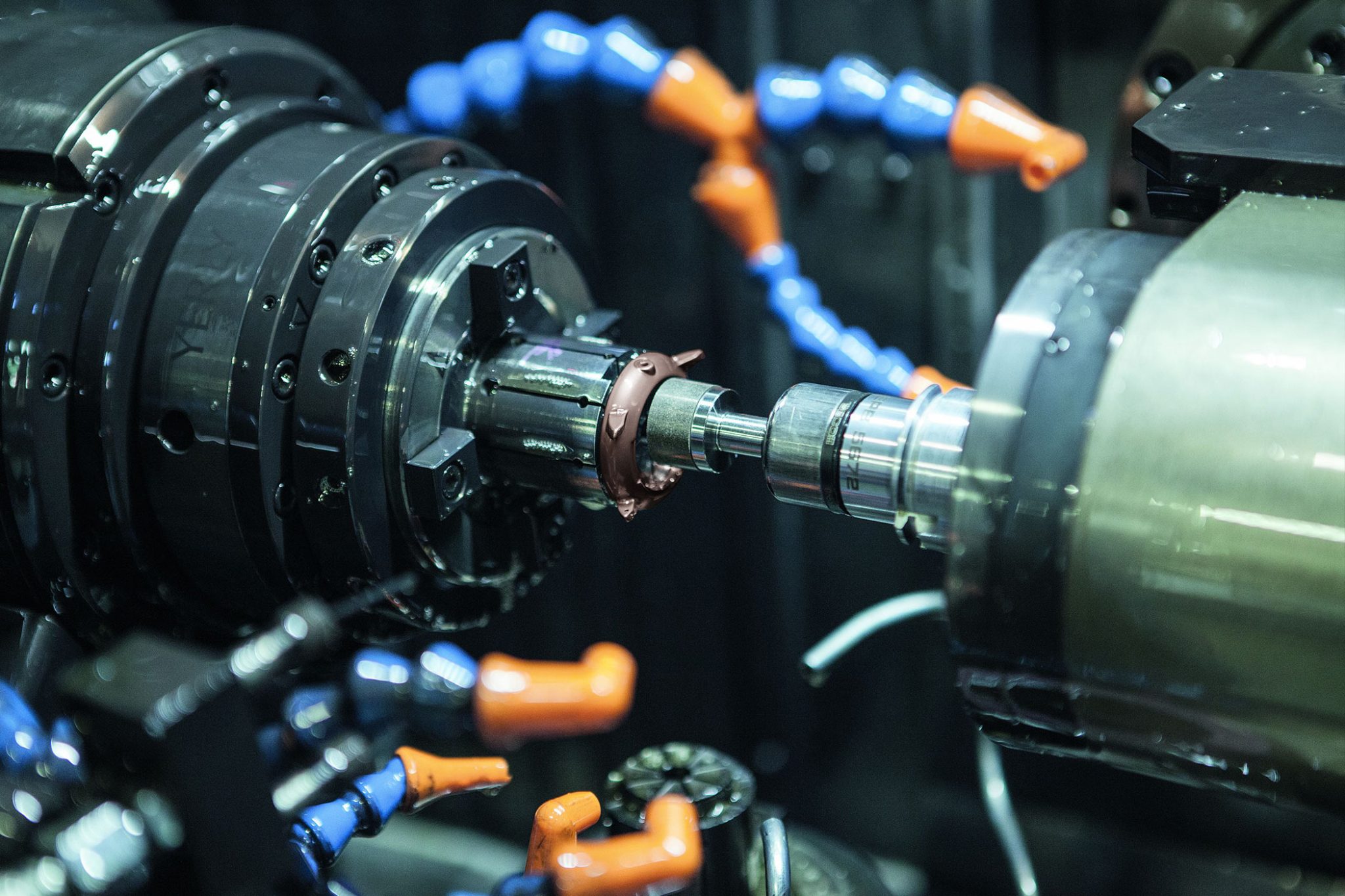
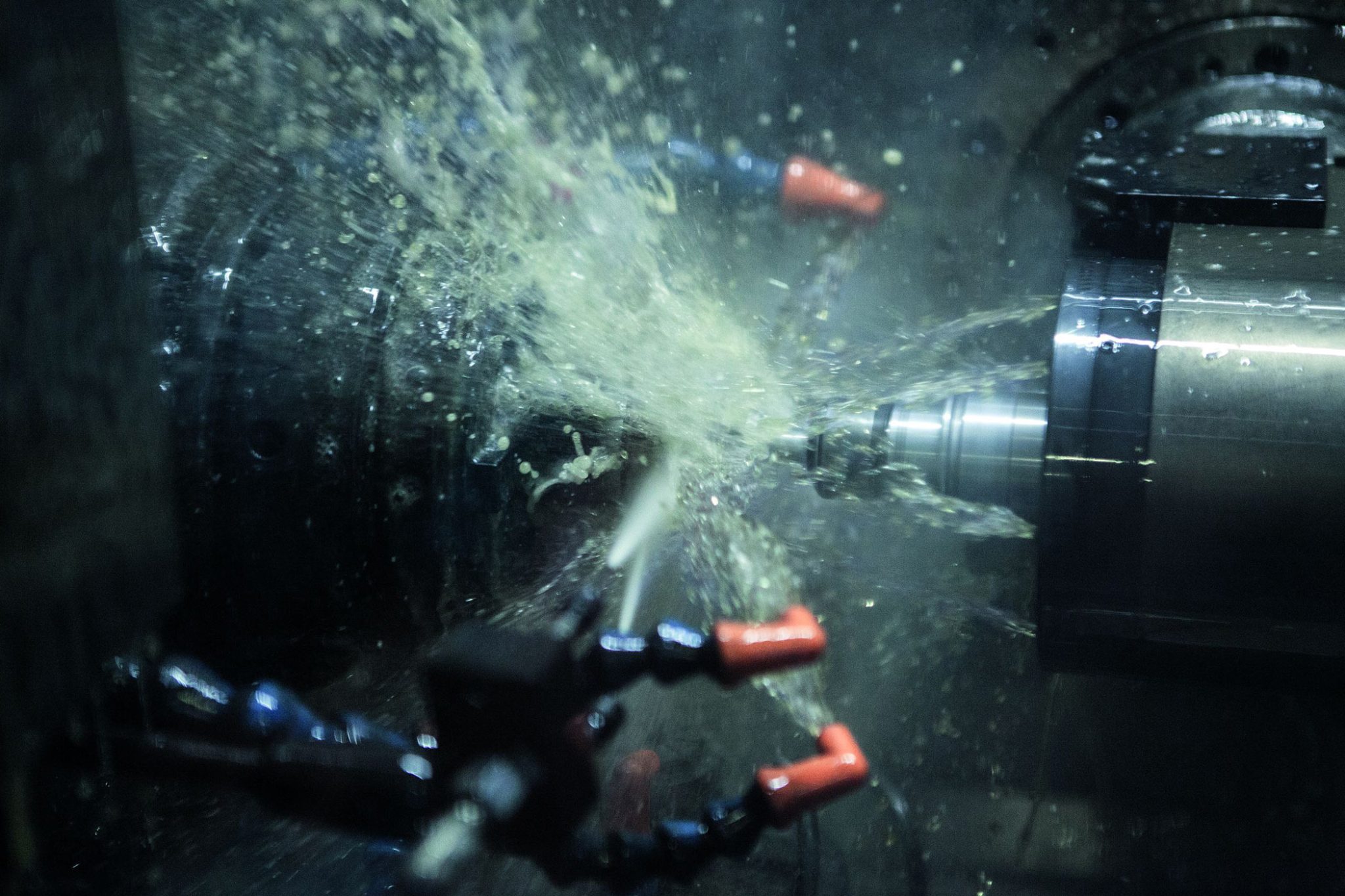
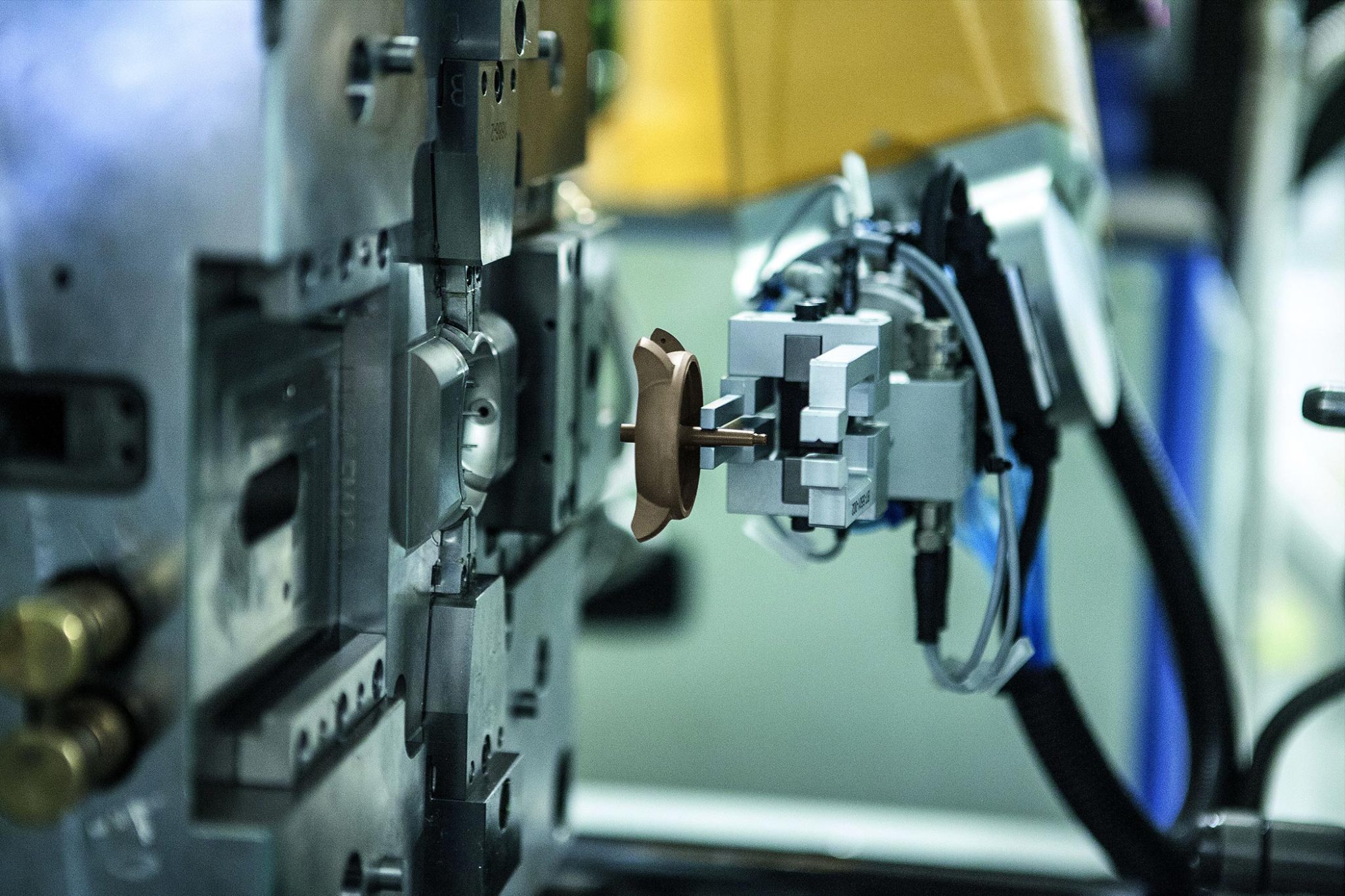
Rados Hightech-Keramik wird in ihrer Manufaktur „Comadur“ in Boncourt hergestellt. Das Wort „Comadur” setzt sich aus den französischen Worten für „Komponenten“, „Material“ und „Langlebigkeit“ zusammen. Die Manufaktur gehört zur Swatch Group und ist daher nicht nur eine Produktionsstätte für Rado, sondern gelegentlich auch für die anderen 16 Marken der Gruppe – von Longines und Omega bis zu Blancpain.
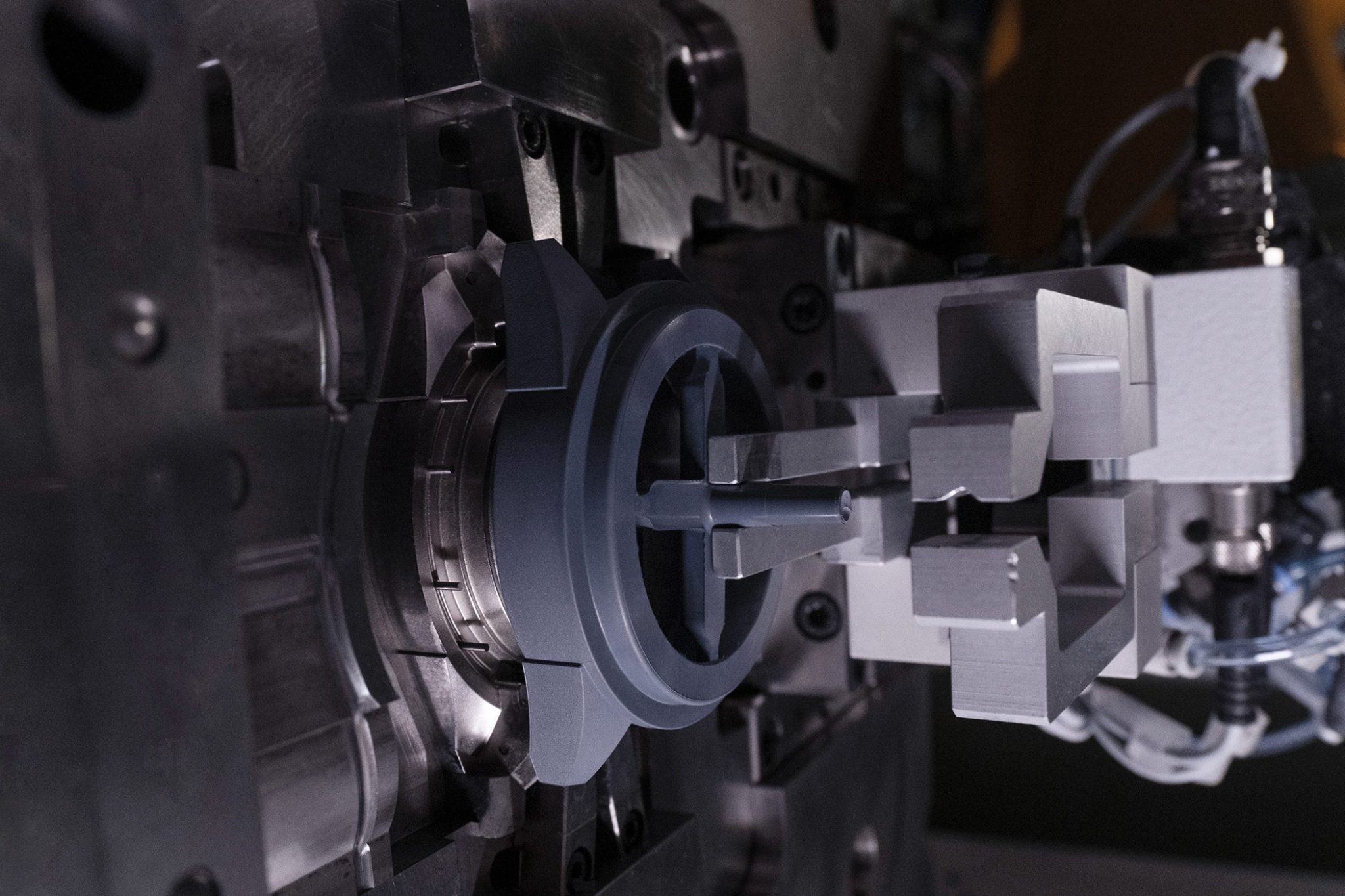
In Comadur konnte ich von Kopf bis Fuß in staubdichte Kleidung und einen Laborkittel gekleidet hinter die Kulissen der Hightech-Keramik-Produktion von Rado blicken. Meine Reise durch die Manufaktur beginnt dabei mit kleinen Kugeln (bestehend aus hochreinem Zirkoniumoxidpulver, Farbpigmenten und einem Polymerbindemittel), die in ein riesiges Vakuum gegeben werden. Anschließend durchlaufen sie die Extrusion und Granulation, wodurch eine dicke Mixtur entsteht, die an Knete erinnert. Nun kann diese Mischung in Formen gegeben werden, die von Rados Designern entworfen wurden. Während dieses langwierigen Teils des Produktionsprozesses können bedeutende Komponenten hergestellt werden. Beispielsweise braucht man für die Herstellung eines Captain Cook Standardmodells nicht weniger als 18 verschiedenen Formen.
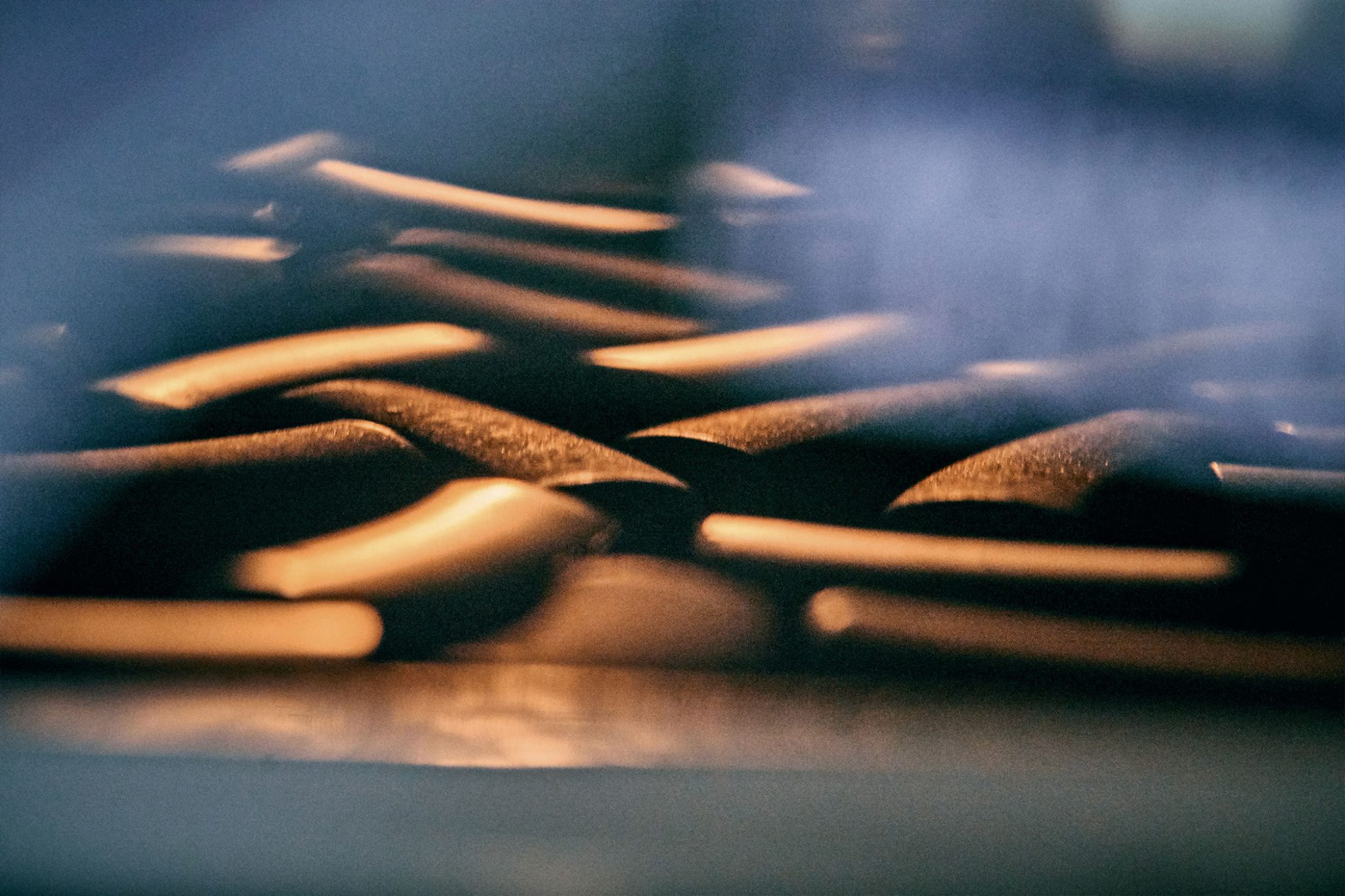
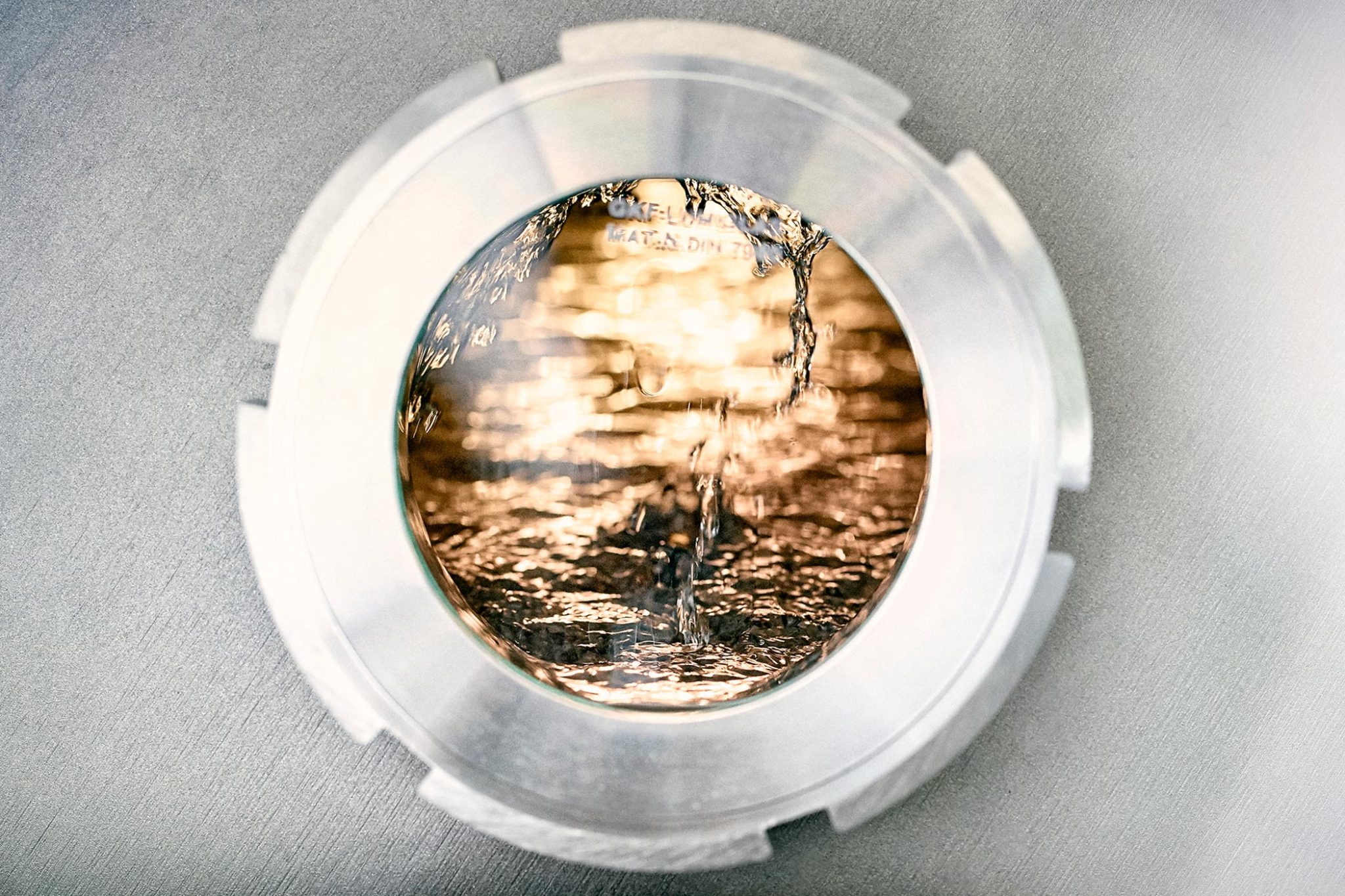
Danach wird das Material einem „Entbindern“-genannten Prozess (dabei werden vor dem Sintern verschiedene Stoffe entfernt) unterzogen. Danach werden die Bestandteile in Alkohol eingelegt, damit der nächste Schritt erfolgen kann: das Sintern. Während des Sinterns erreicht die Keramik eine Vickershärte von 1.250 (zum Vergleich: Edelstahl besitzt eine Vickershärte von nur 180). Die Stücke werden in den 1.450 Grad Celsius heißen Ofen gegeben, wobei die Temperatur je nach gewünschter Farbe leicht variiert und die Komponenten um fast 25 Prozent schrumpfen.
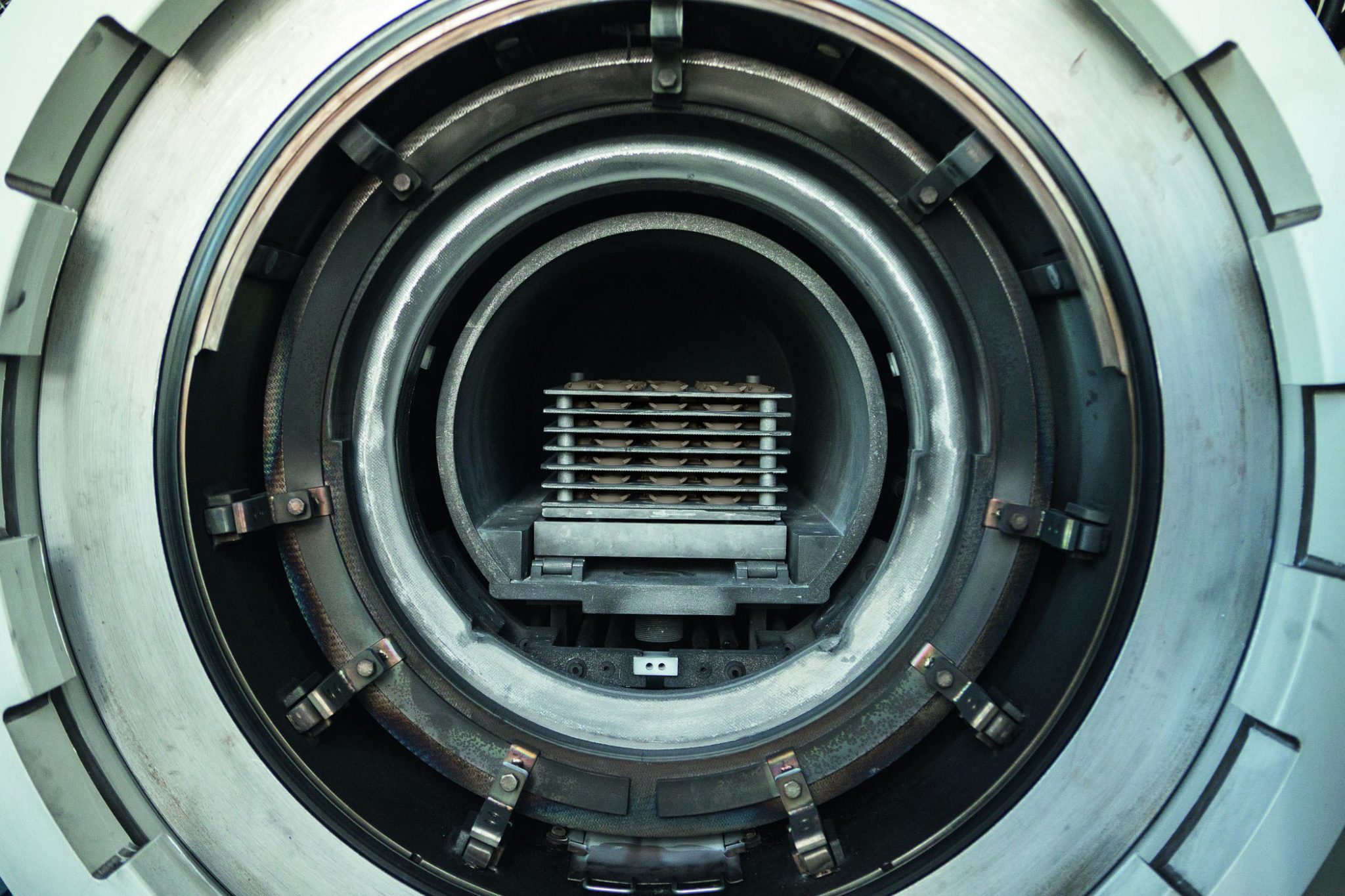
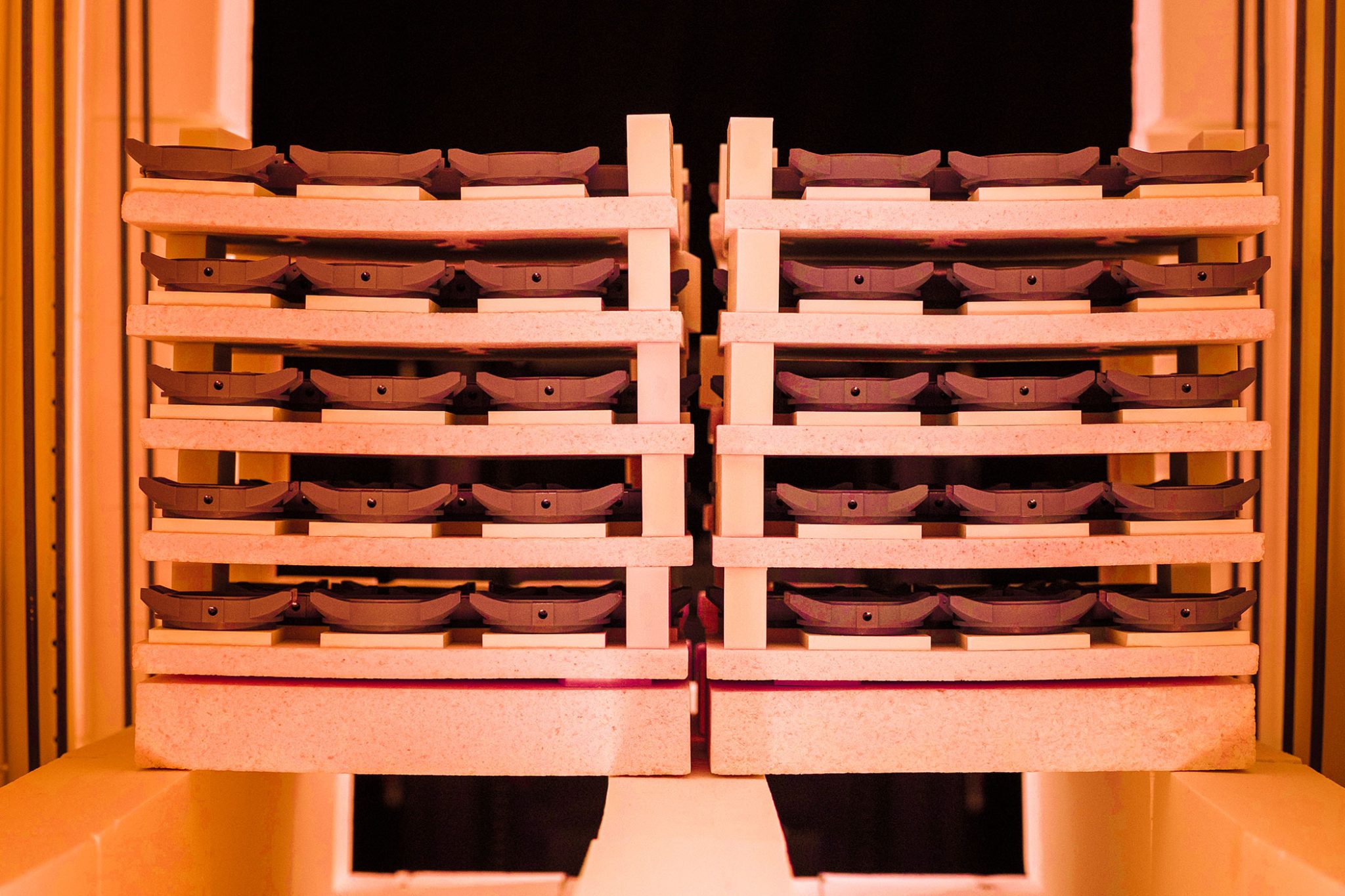
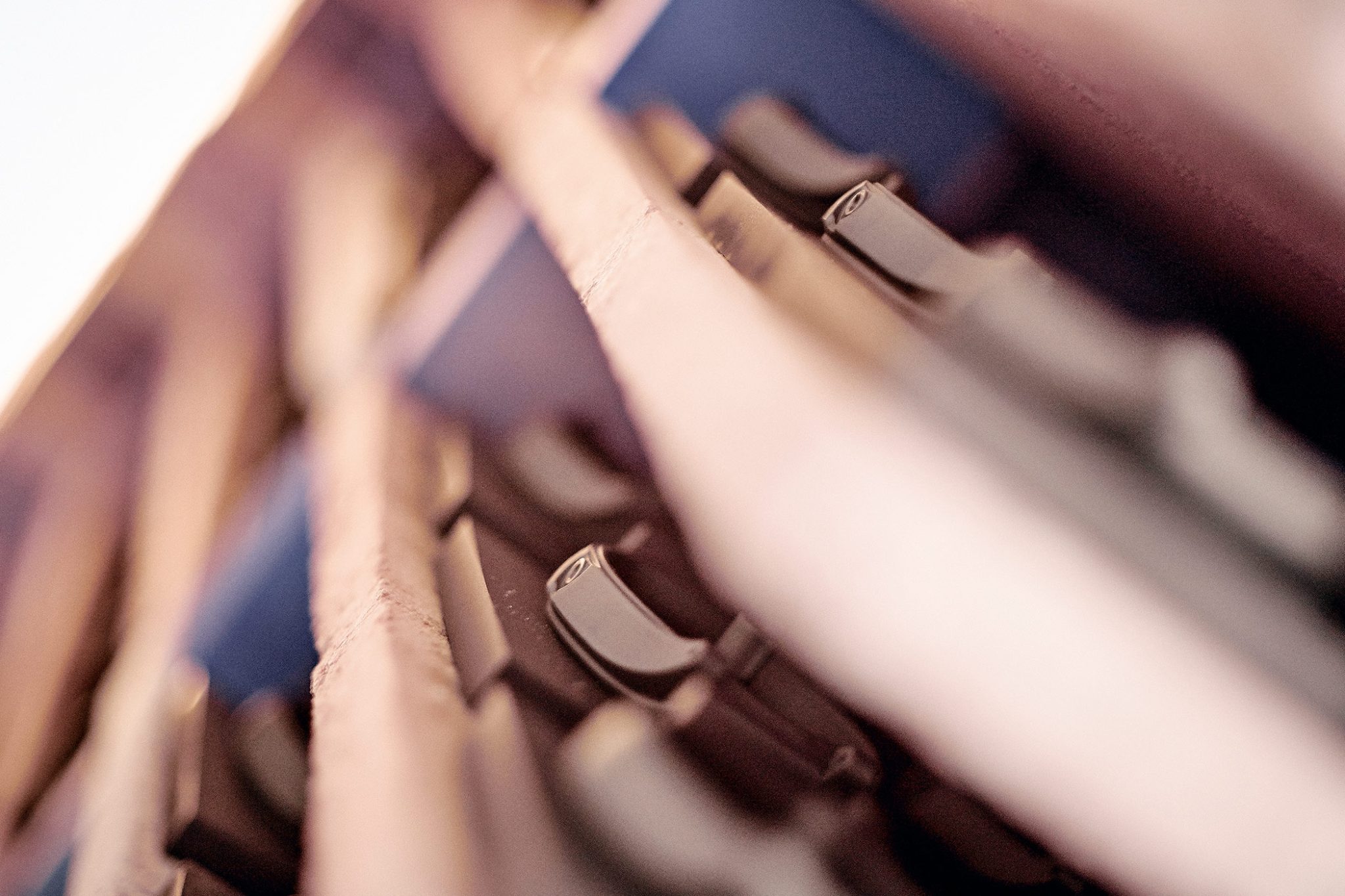
Die gewünschte Farbe der Keramik entsteht vor allem während der Zeit im Ofen. Erst nach Abschluss des Sinterprozesses zeigt sich die tatsächliche Farbe: Rot ist beispielsweise vor dem Sintern weiß, während Gelb zunächst grau ist. Nachdem die keramischen Bauteile durch diesen Prozess die Form des Endprodukts angenommen haben, können sie nun maschinell bearbeitet werden. Aufgrund der Härte der Keramik ist dies ein komplexer und zeitaufwändiger Prozess: Während die Bearbeitung von Stahlteilen nur etwa drei Minuten dauert, benötigen Keramikteile eine Stunde. Außerdem müssen die Gehäuse mit einer Diamantscheibe bearbeitet werden, also mit einem Material, das härter als Keramik ist. Das Polieren der Keramik (bei dem die Teile in ein Bad aus kleinen Keramikfragmenten getaucht werden) gestaltet sich auch nicht wirklich einfacher und dauert eine ganze Woche. Nachdem die Gravuren auf die Lünette gelasert wurden, erfolgt die Lackierung der Rado-Uhren von Hand.
Plasma-Keramik
Während diese Schritte alle für die unverwechselbaren Hightech-Keramikuhren von Rado gelten, bevor sie zur Montage und Kontrolle geschickt werden, ist für die unverwechselbare Metallfarbe der Plasma-Keramikuhren der Marke ein anderer Ansatz erforderlich.
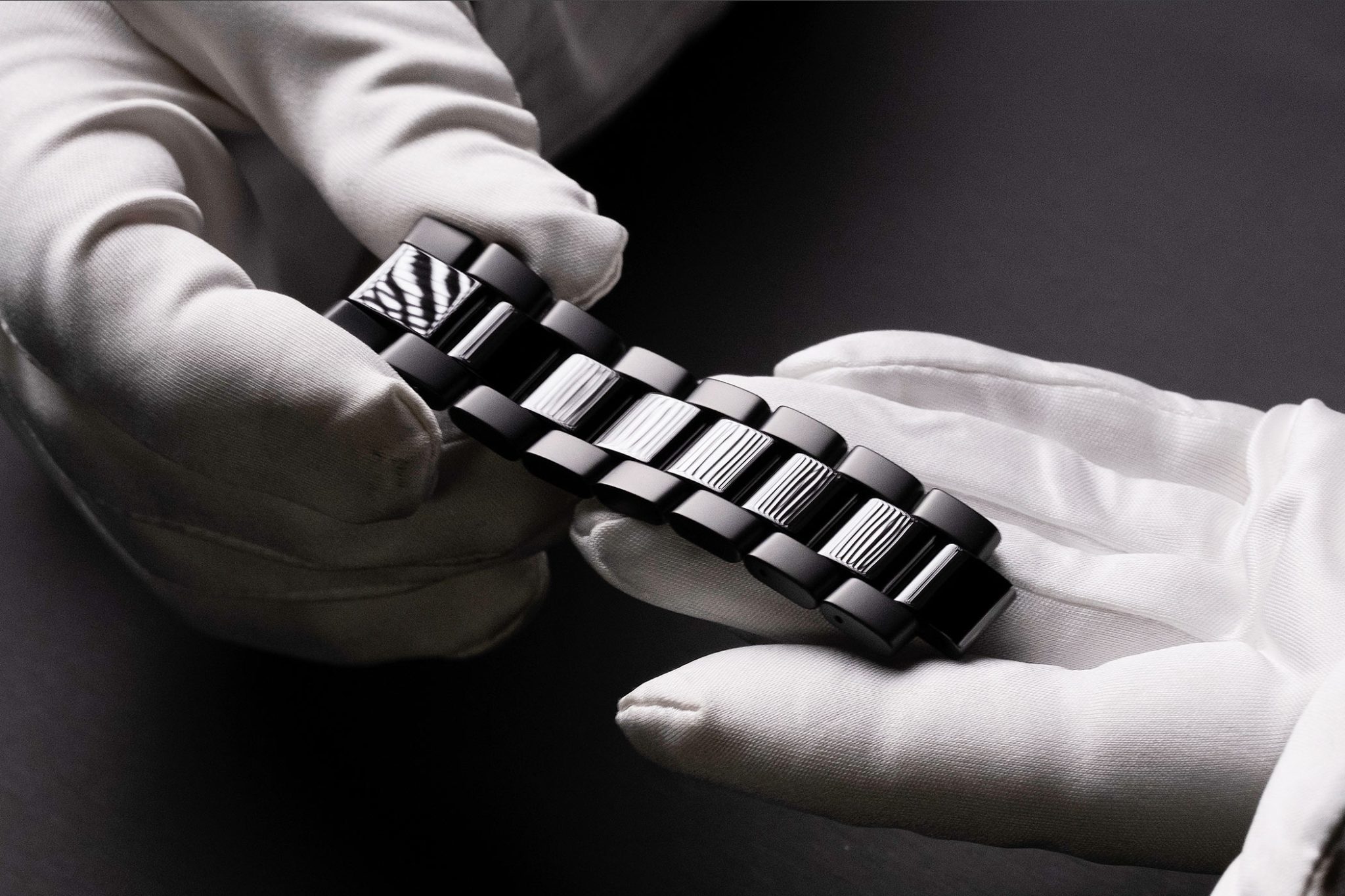
Bei diesem zusätzlichen Schritt werden vorpolierte weiße Keramikteile in eine Plasmasäule eingelegt, auf nicht weniger als 20.000 Grad Celsius erhitzt und verbleiben drei Stunden lang in der Säule. Dieser „Plasma-Aufkohlungsprozess“, den Rado seit der Lancierung der Ceramica im Jahr 1998 anwendet, verändert zwar die chemische Zusammensetzung der Keramik, ihre Eigenschaften bleiben jedoch unberührt. Dadurch sind die Plasma-Keramik-Uhren so hart, kratzfest, leicht und hypoallergen wie alle anderen bei Rado hergestellten Keramikuhren, mit einem sehr ausgeprägten metallischen Aussehen.
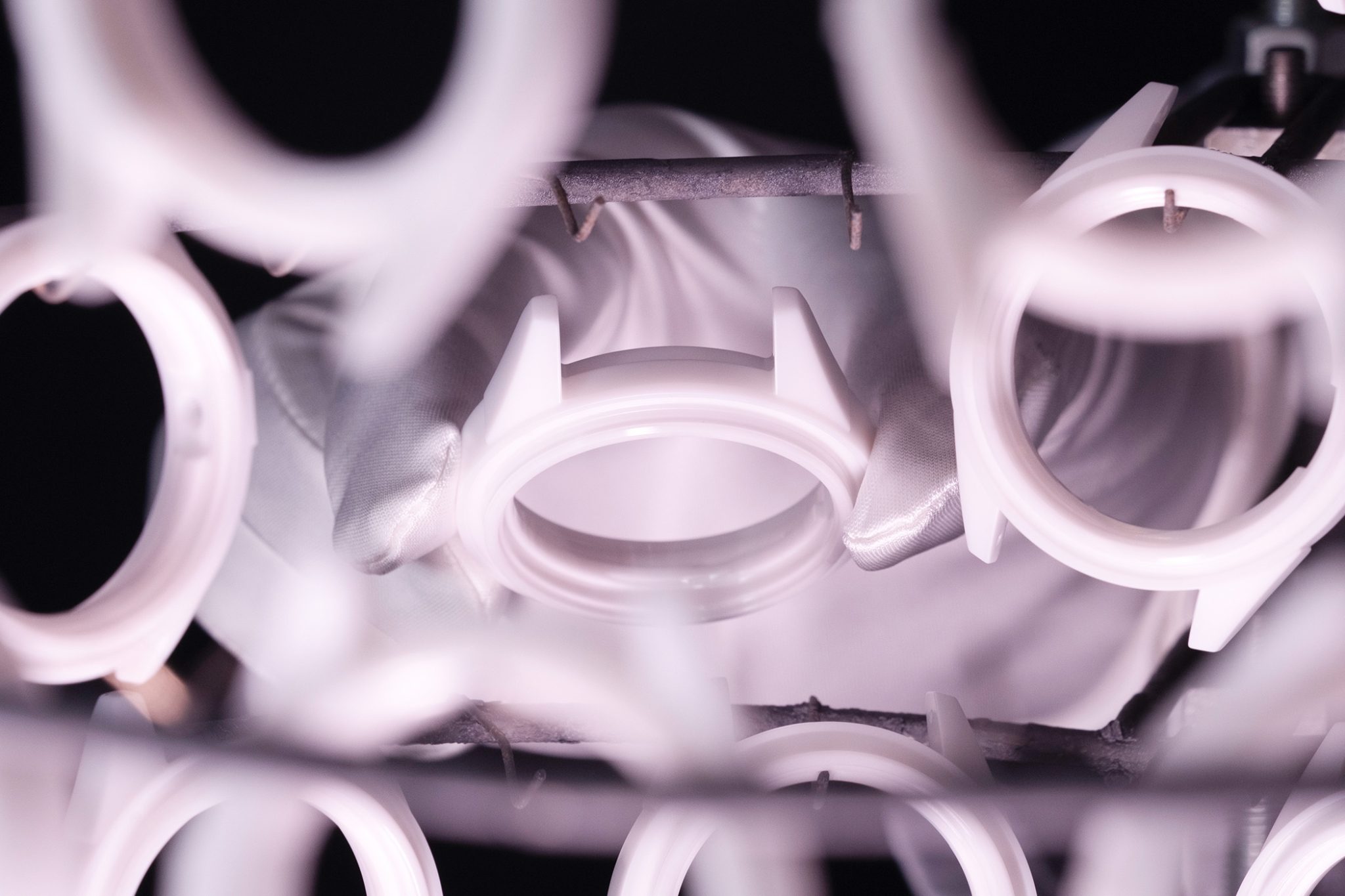
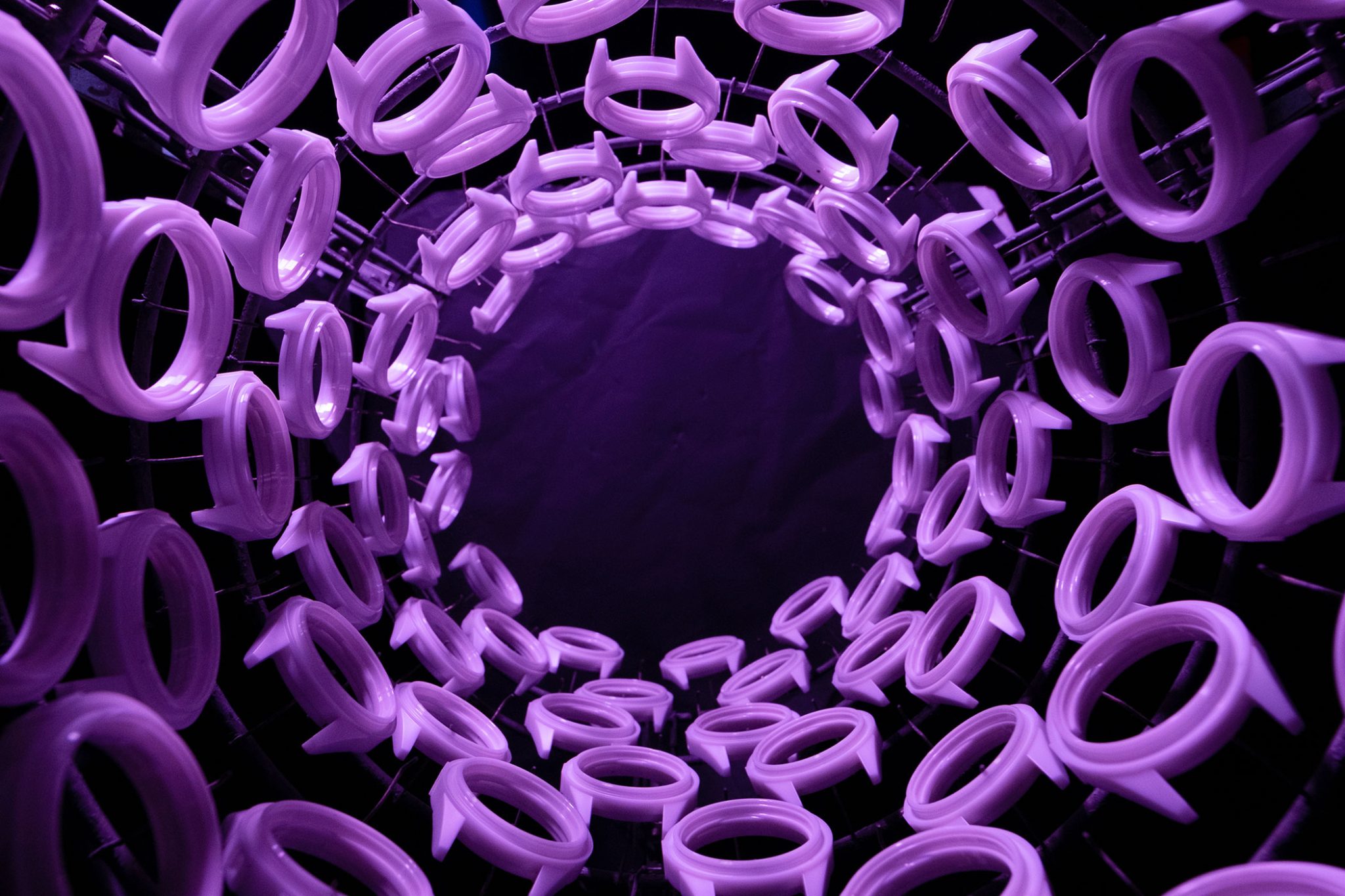
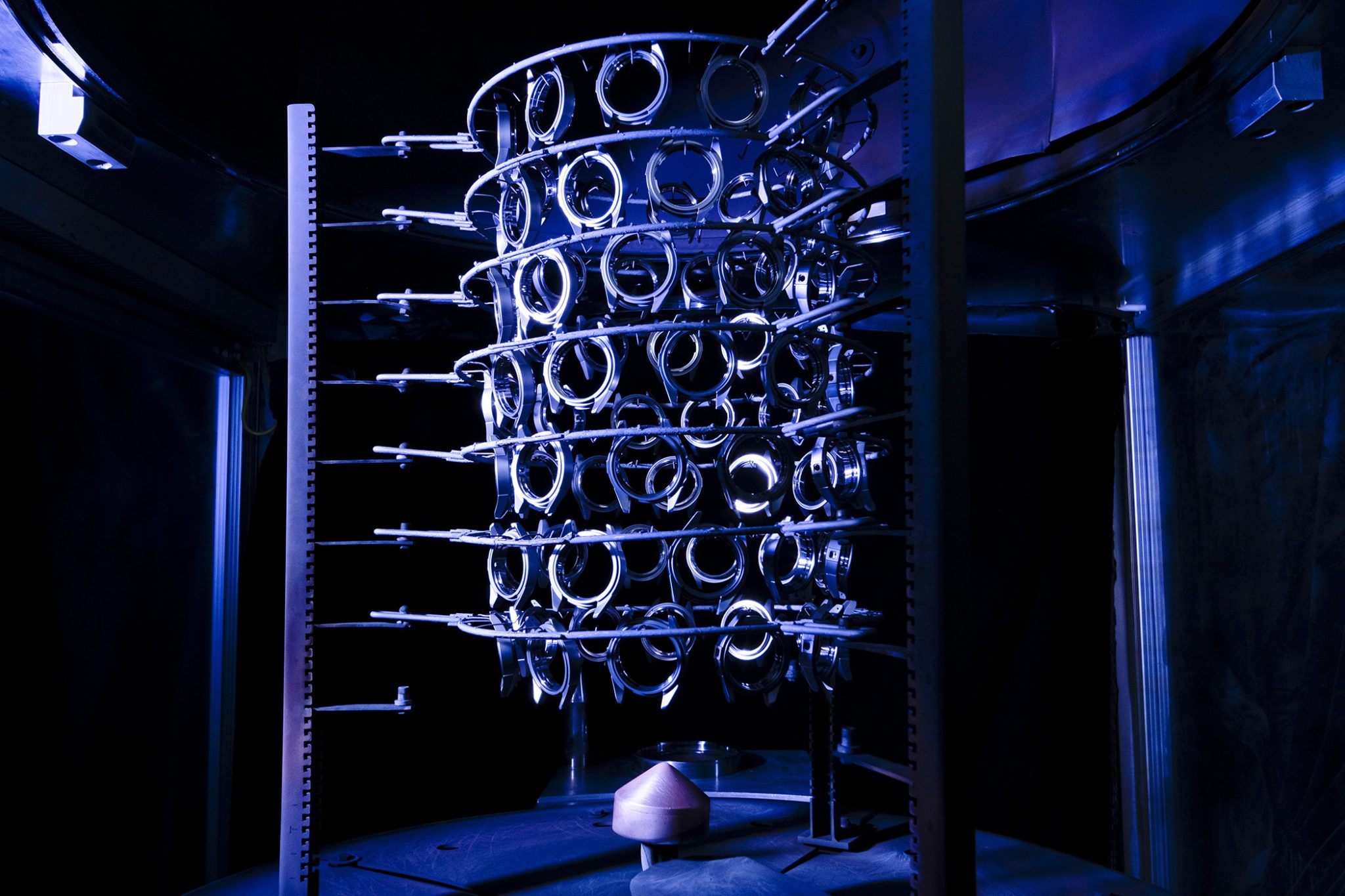
Die Schlüsselrolle der Rado Diastar 1
Die Rado Diastar war der erste kratzfeste Zeitmesser der Welt und zukunftsweisend für die Branche. Mit ihr erreichte Rado mehrere Meilensteine. Dazu gehören die Konzeption und Einführung von Materialien wie Ceramos, Saphirglas und Hartmetall, die wir alle näher in Augenschein nehmen sollten.
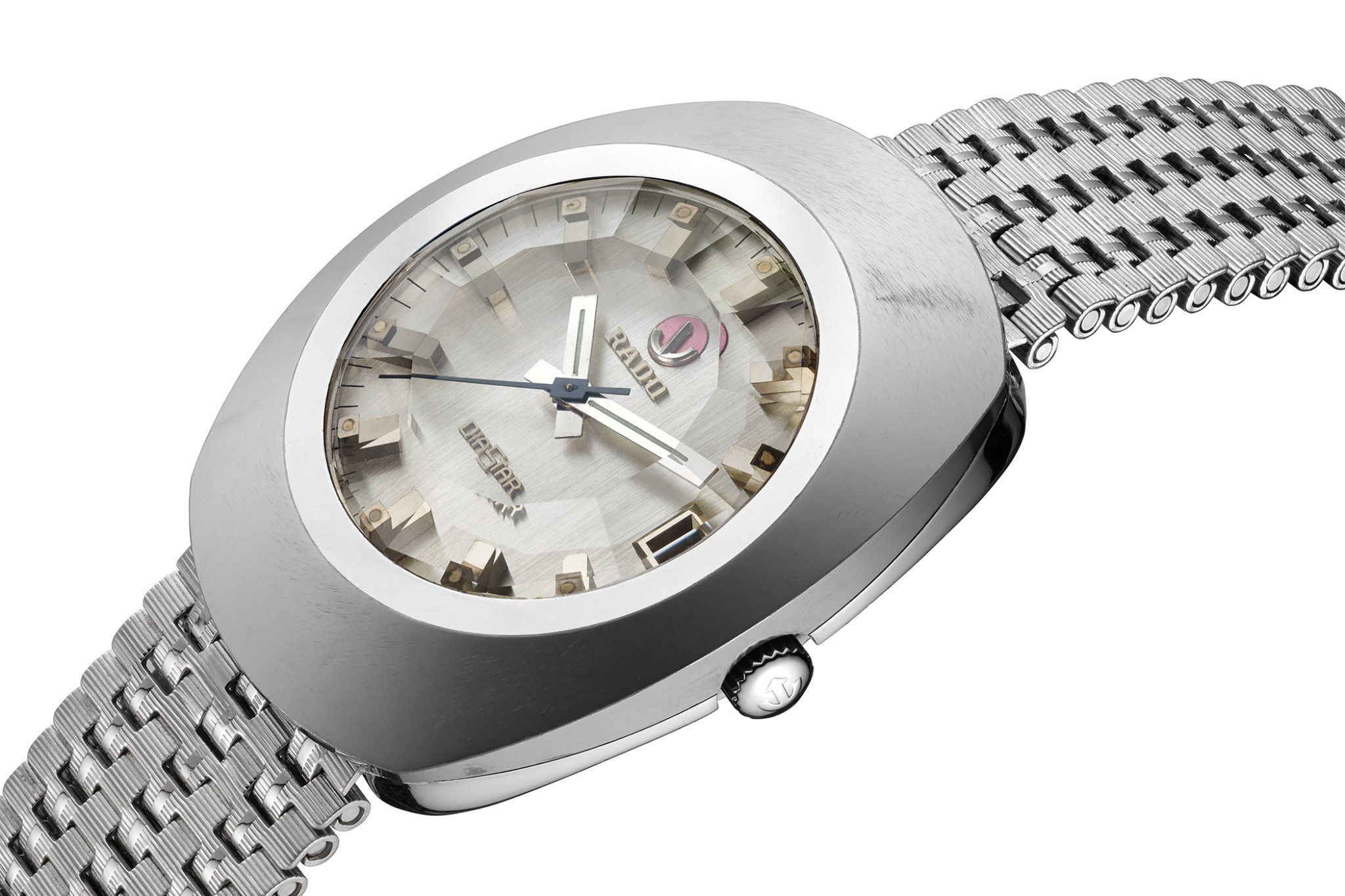
Ceramos
Entgegen allem Anschein handelt es sich bei Plasma-Keramik um kein Metall. Ein innovatives Verbundmaterial von Rado nutzt aber Metall: Ceramos kombiniert die Härte von Keramik (etwa 90 Prozent Titankarbid) mit dem Glanz einer Metalllegierung. Dadurch wird nicht nur die Kratzfestigkeit erhöht, sondern auch das Gewicht der Uhr verringert. Der bekannteste Ceramos-Zeitmesser ist sicherlich die im letzten Jahr wieder eingeführte Diastar Original. Dieses Modell bietet auch die perfekte Überleitung zu unserer vorletzten Station auf den Spuren von Rados Weg zum Titel „Master of Materials“: Rados Arbeit mit Saphirglas.
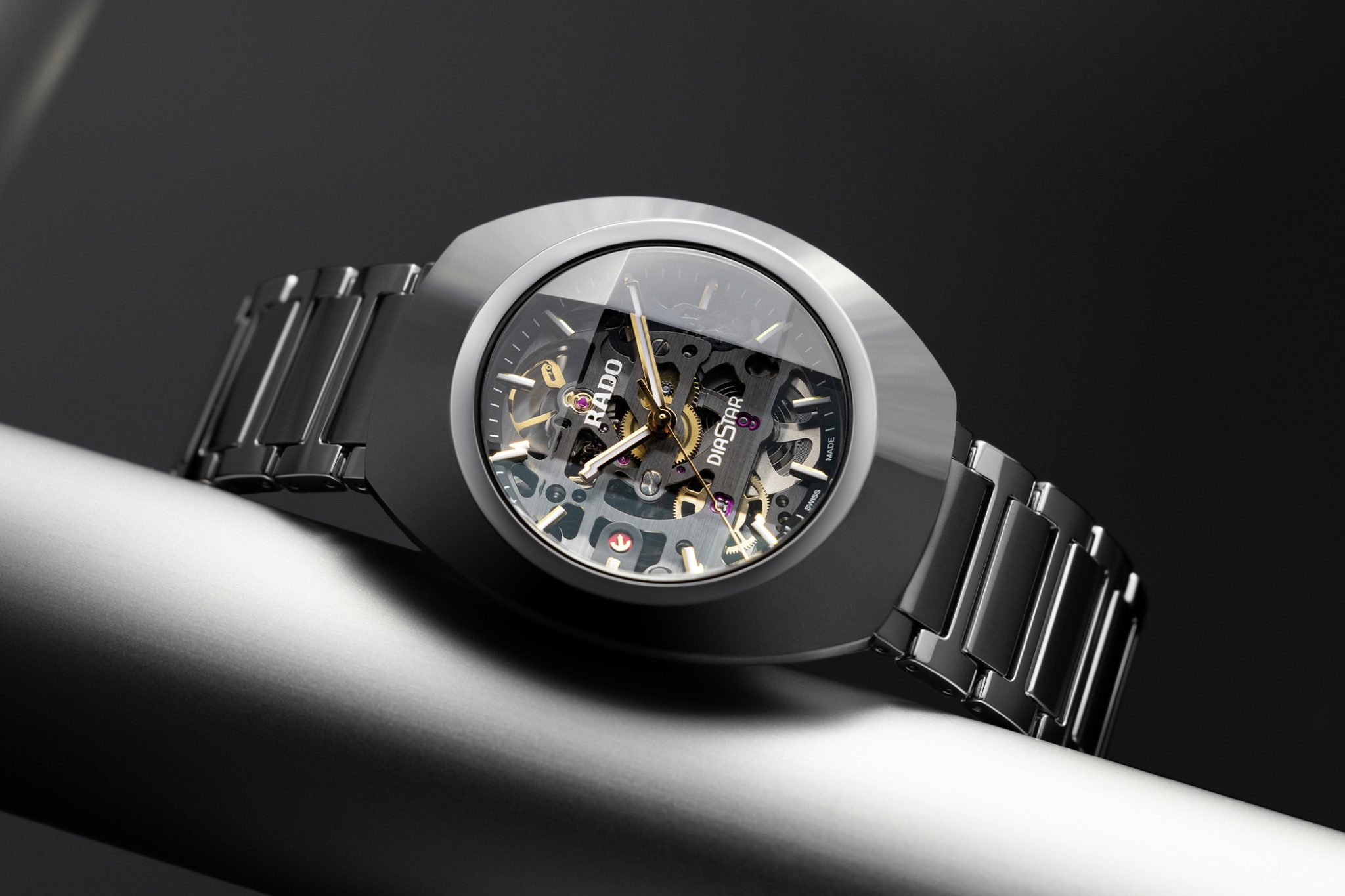
Saphirglas
Saphirglas ist eines der härtesten Materialien, die es gibt. Allerdings erhielt es erst in der zweiten Hälfte des 20. Jahrhunderts in großem Stil Einzug in die Uhrenindustrie, als es für viele Marken noch üblich war Plexiglas zu verwenden. Doch Rado sollte die Schweizer Luxusuhrenbranche im Jahr 1962 mit der Lancierung der unverwechselbaren DiaStar1, die in großen Mengen produziert wurde, maßgeblich verändern. Rados Einsatz von Saphirglas geht aber über die Ergonomie hinaus, denn die Marke erforschte auch, wie man die Ästhetik der Rado-Uhren mithilfe des Materials verbessern kann.

So hat sich Rado seit 1976 auf „Rand-zu-Rand“ Saphirglas spezialisiert. Während bei den meisten Uhren das Saphirglas bis zur Lünette reicht, erstreckt sich das „Rand-zu-Rand“-Saphirglas über das gesamte Gehäuse. Darüber hinaus versieht Rado das Saphirglas einiger seiner Uhren mit markanten geometrischen Formen. Dies ist kein einfacher Prozess, denn die Bearbeitung und das Schleifen muss mit Hilfe von Diamantwerkzeugen sorgfältig ausgeführt werden.
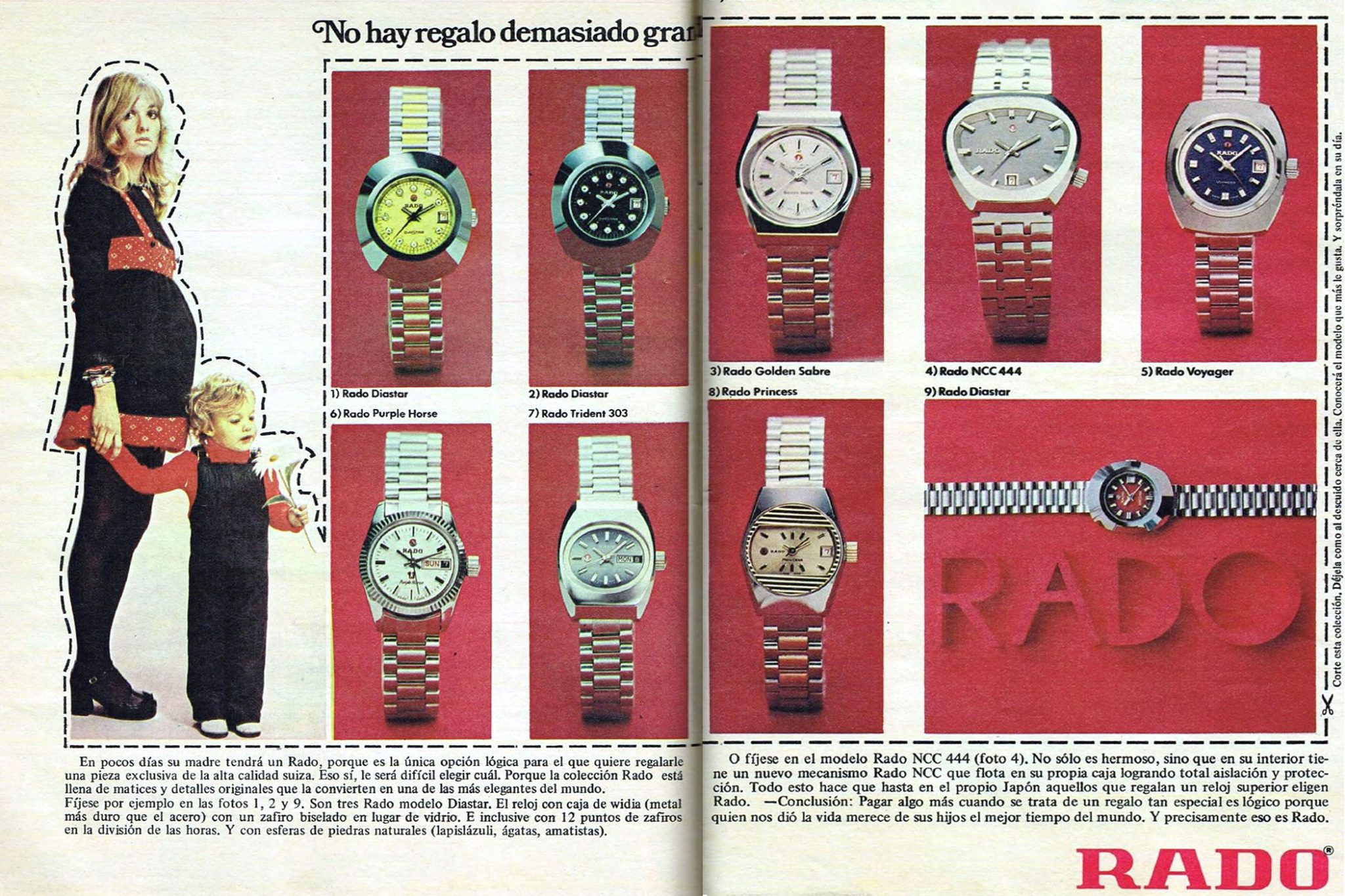
Hartmetall
Hartmetall kann als Vorläufer von Ceramos angesehen werden: die erste DiaStar, die 1962 eingeführt wurde, verwendete dieses Material. Hartmetall besteht aus Keramik (Wolframkarbid) und einem Metallbindemittel und bietet sowohl die Härte von Keramik mit der Widerstandsfähigkeit von Metall, als auch eine hochglänzende Oberfläche.
“If we can imagine it, we can make it. And if we can make it, we will.”
Meine kurze Reise nach Comadur kratzt allerdings nur an der Oberfläche von Rados Errungenschaften im Gebiet der Materialien. Viele ihrer Modelle haben die Standards in der Branche herausgefordert – von der eSenza (der ersten Uhr ohne Krone) über die V10K, die aus Hightech-Diamanten gefertigt ist und damit die Härte von Diamanten aufweist, bis hin zu unerwarteten Neuheiten, die mit photochromem Glas experimentieren. All das zeigt, dass der Kreativität und Ambition von Rados Designern keine Grenzen gesetzt sind.
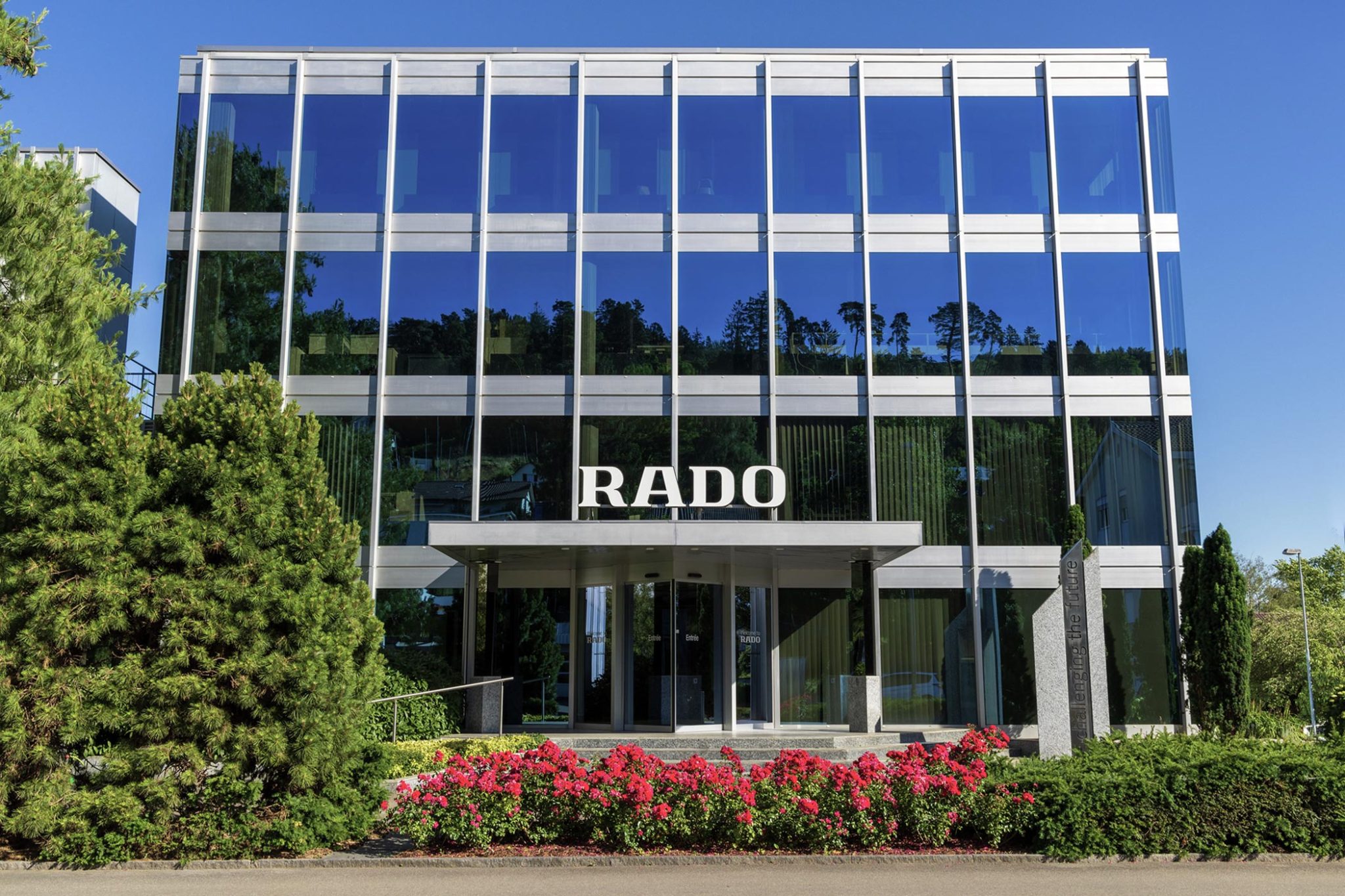
Rados Entscheidung, sich weitgehend nur auf ein einziges Material (Hightech-Keramik) zu fokussieren, ist ebenfalls ein wesentlicher Aspekt ihres Markenkerns. Egal, ob man eine Uhr sucht, mit der man ohne Angst vor Kratzern auch einmal irgendwo anstoßen kann, oder eine, die sich glatt und geschmeidig anfühlt – vermutlich beruht ein Großteil von Rados Erfolg darauf, dass die Leute genau wissen, was sie von einer Rado-Uhr erwarten können. Das ist sicherlich ein echter Vorteil in diesen für Verbraucher unberechenbaren Zeiten.
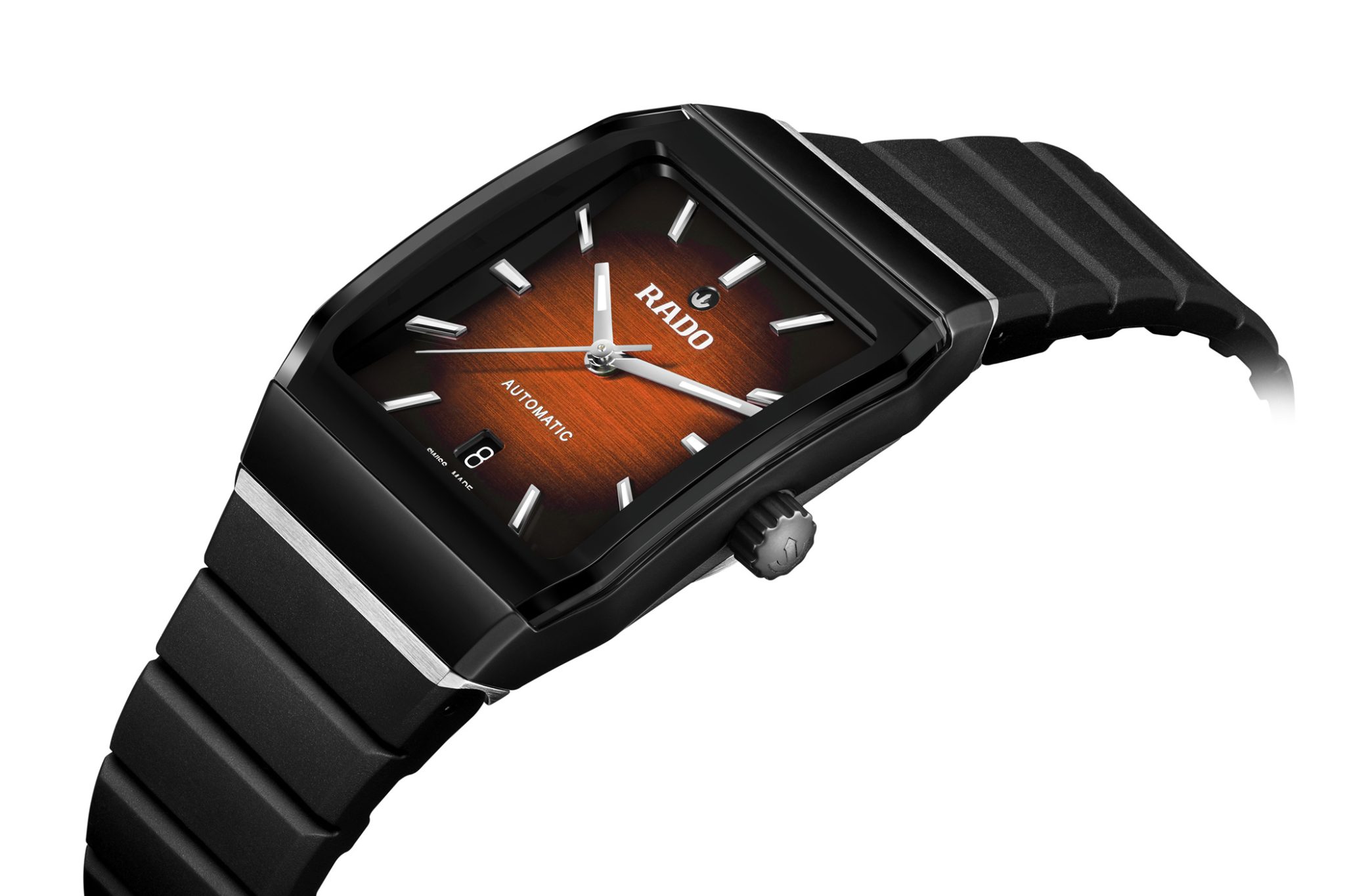
Was auch immer der Grund für Rados stetig wachsenden Erfolg sein mag – seit Jahrzehnten etwa auf dem sich schnell entwickelnden indischen Markt –, wir können zweifellos Großes von einem Uhrenhersteller erwarten, der ständig danach strebt, seine Träume zu verwirklichen. Womöglich können wir alle etwas daraus lernen.